Powdercoat Paint Processing Colours
Standard Powdercoat Paint Finishing Colours
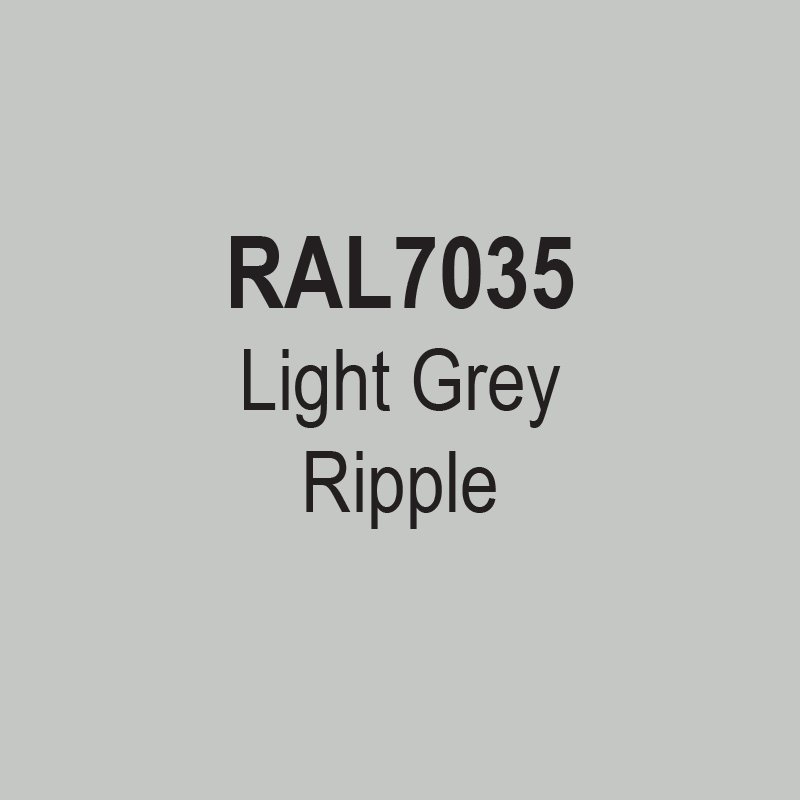
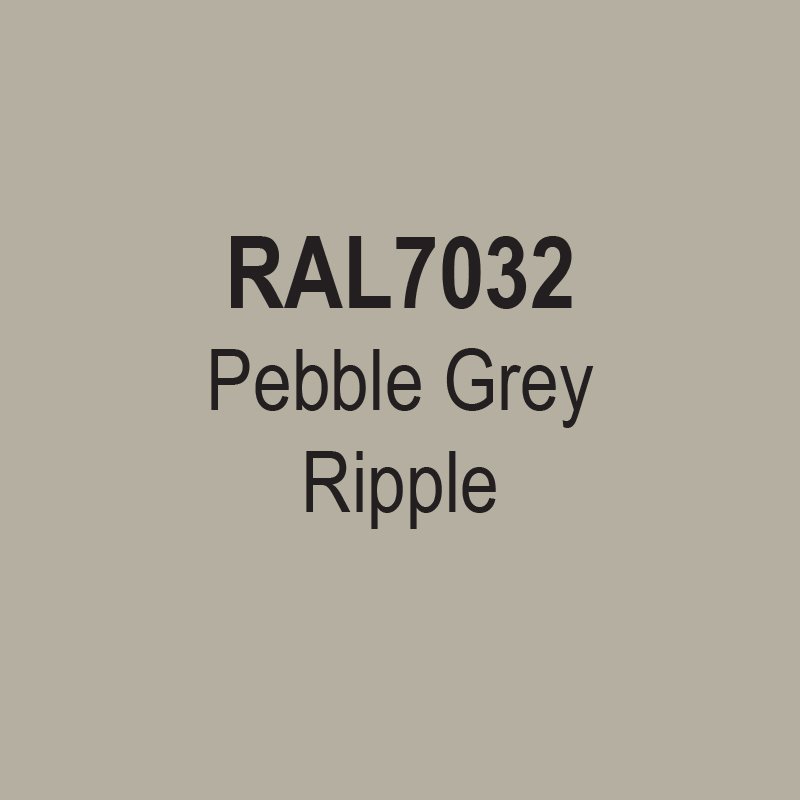
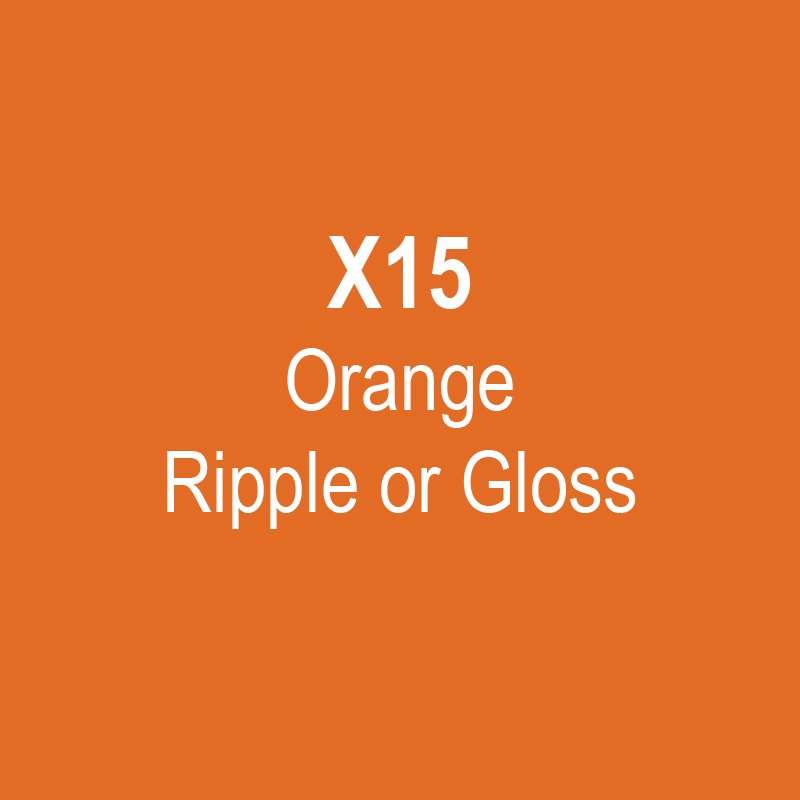
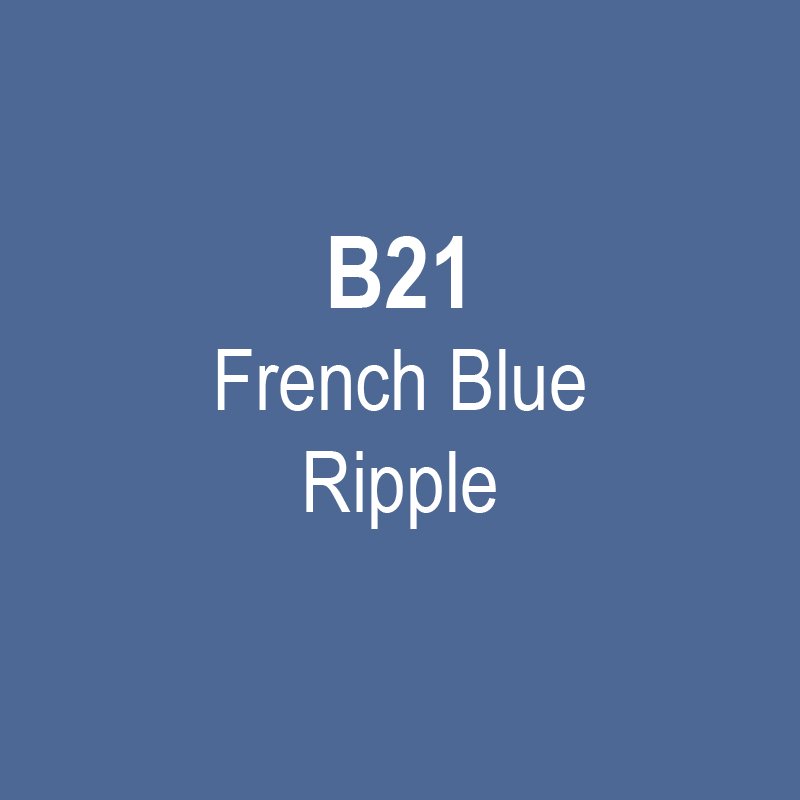
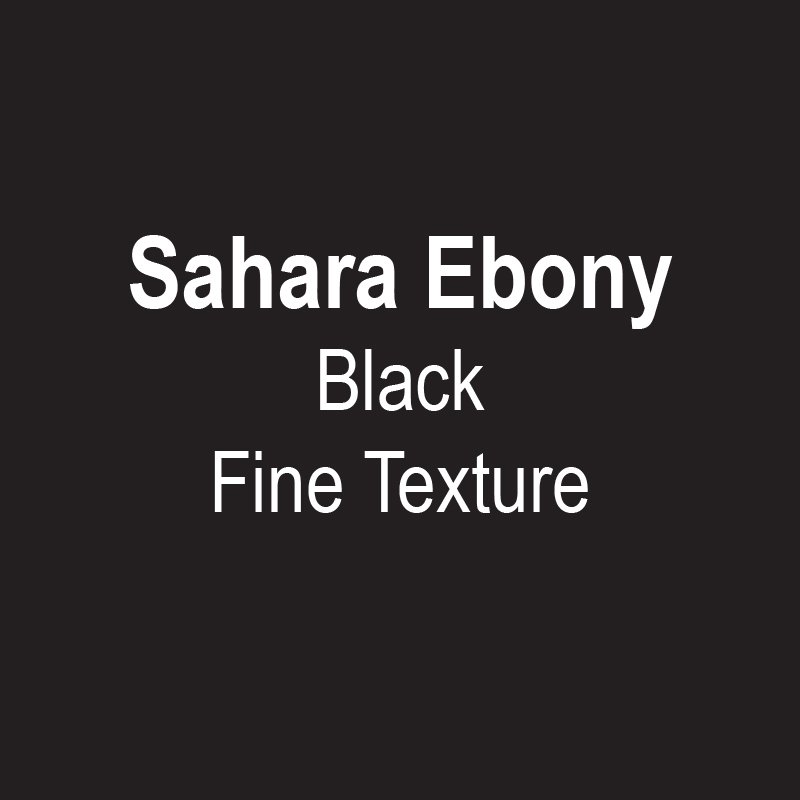
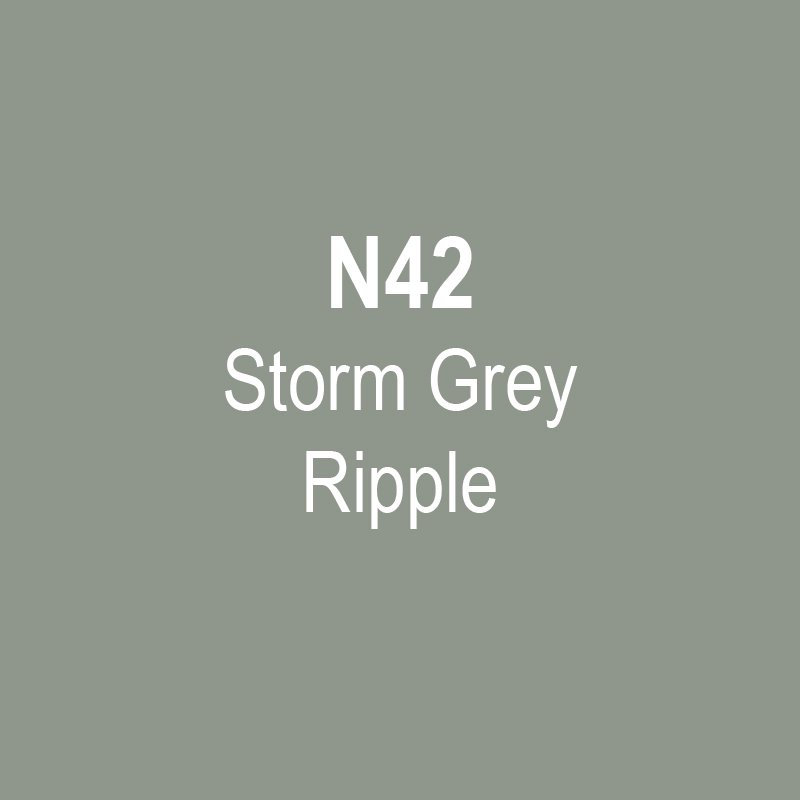
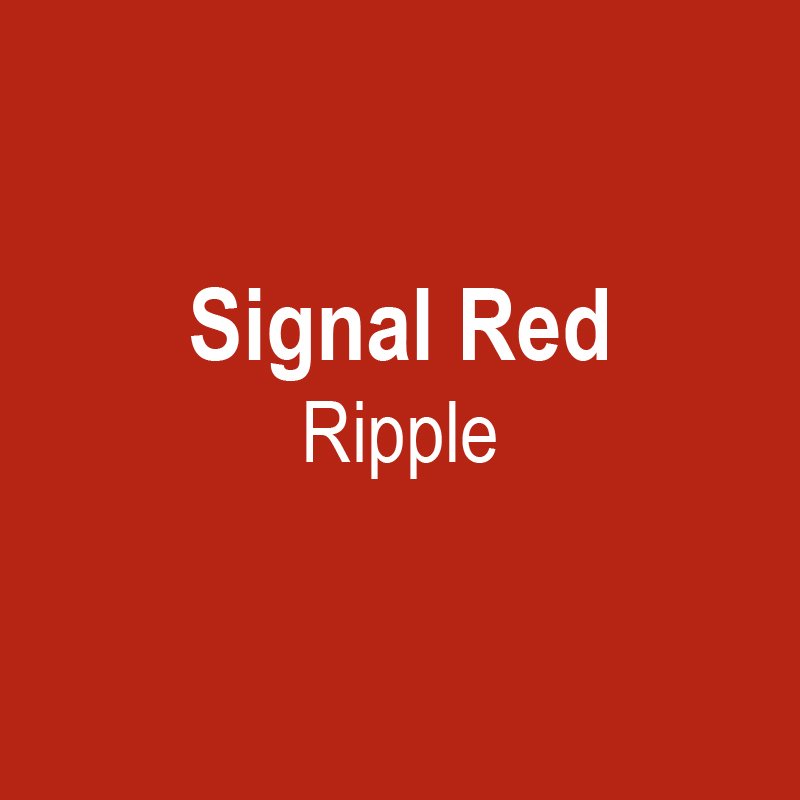
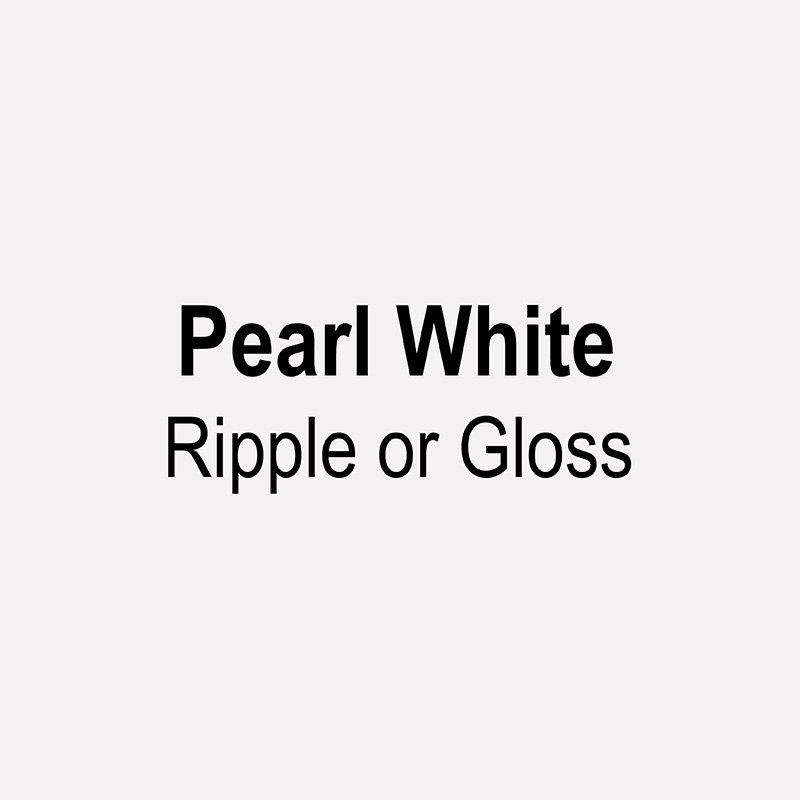
Please note: Actual colour may vary from on-screen representation. If you are unsure, please contact your local sales office to discuss your colour choice prior to purchase.
B&R offer a range of standard powdercoat colours and finishes on all of our electrical enclosures. Other colour options are available on request. Contact one of our sales representative to discuss your powdercoat colour options.
We use the electrical industry colours of Light Grey (RAL7035) and Pearl White. Enclosures and external components are powdercoated in Light Grey with a ripple finish. Pearl White Gloss is used for internal components only. Pearl White Ripple is available for enclosures and external components.
All metallic powdercoated enclosures manufactured at B&R are powdercoated using a modified polyester paint and conform to the following in-process testing. All test results are recorded and audited in accordance with our Quality System (ISO 9001: 2015).
The Pre-Treatment Process
The majority of B&R’s powdercoated products are manufactured from zinc coated steel. This has a continuous hot dipped zinc coating (20 microns) added to the raw material, giving added corrosion resistance. The pre-treatment process itself consists of four stages.
Stages one and two are both cleaning stages, which remove all unwanted oils and grease and apply a protective coating of Iron Phosphate. The Iron Phosphate provides an insulating barrier on the surface of the metal, which also improves the adhesion and ensures an even and consistent coverage.
Stage three is a rinse tank with pressurised recirculated fresh water.
Stage four consists of a final sealing rinse.
Titration Tests are conducted on both Phosphate tanks, to ensure that the values recorded meet the specifications that have been agreed in consultation with our pre-treatment chemical and powdercoat suppliers.
Powdercoating Thickness Test
Powdercoat paint is applied to the steel at an average coating of 100 microns for ripple finish and 70 microns for gloss finish. The minimum coating thickness is 90 microns on the exterior, and 60 microns on the interior of the enclosure, which conforms to AS/NZS 4506:2005.
The paint thickness tests are conducted regularly, to a specified frequency, using a calibrated paint inspection gauge.
The method of testing complies with the requirements of AS 1580.108.1:1994.
Cure Test (Solvent Resistance Method)
Using a cure test solvent, the powdercoat paint is tested to differentiate between cured and under-cured powdercoatings. The test has been developed in consultation with our powder coating suppliers, and incorporates the comparison of the test results with known cured panels.
The method of testing complies with the requirements of AS/NZS 4506:2005.
Adhesion (Cross Cut Test)
This test is conducted to confirm that the adhesion properties satisfy the requirements of AS/NZS 1580.408.4:1993.
Paint Colour Comparison Test
All powdercoat colours used by B&R Enclosures are inspected every time they are used. and visually compared to approved standard colour samples.
The samples themselves are calibrated, to ensure that they match the colour standards specified in AS 2700-2011, or an approved customer supplied sample.